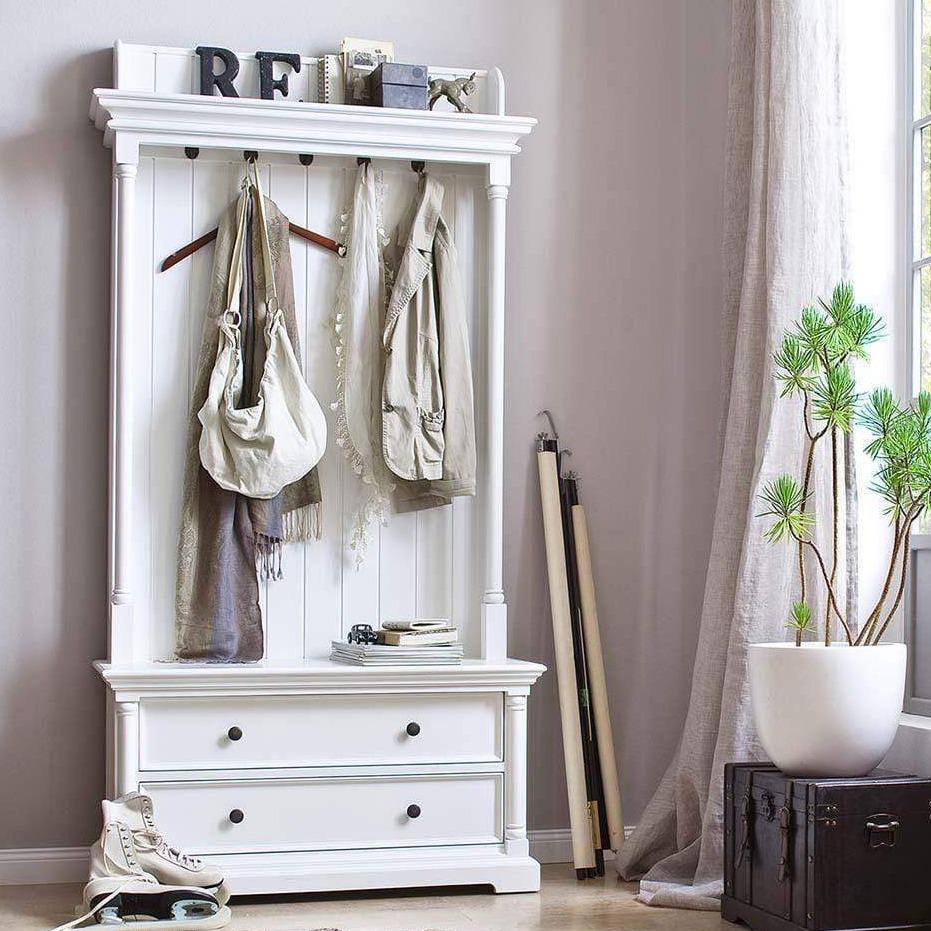
HOW OUR HALIFAX AND PROVENCE FURNITURE RANGES ARE MADE
Watch Video
Caring about and understanding how we manufacture and distribute our furniture is important to the end story. When was the last time we stopped to think about how the furniture items we are about to purchase, were made? Here is some brief information that can start to answer some of those questions.
All our timber, composites and rattan components, used in the production of our furniture have been tested to comply with international standards and fulfil the requirements of sustainable forest production management. The paint used in the finishing and hardware accessories comply with Australian health and safety standards.
Each piece of furniture is designed and manufactured at the overseas factory using only high-grade materials, machinery and craftsmanship to ensure a quality product. We make sure the factory takes a hands-on approach from the selection of ethically sourced timber through to the seal of each packed carton.
The timber used in our furniture is ethically sourced from approved plantations; nothing ever comes from natural forests. Because the Halifax range is exported globally, furniture items must adhere to the strictest compliance standards set by the European, North American and Australian governments. This includes composites used in the furniture such as MDF (medium density fibre board) that has passed the safest CARB rules.
Each piece is packed in triple craft 275g (7-layer) overlapping carton boxes. All surfaces are lined with foam wrap. All corners and edges are protected with contoured Styrofoam bricks. 3-piece MDF caps to withstand impact further reinforce the corners. A final 2.5cm thick piece of Styrofoam is placed on the top surface that runs the length of the box. The furniture is then sent in their customized boxes, with labels clearly identifying the orientation (up, down, front, rear) for proper handling. You can watch our video to see how easy it is to unpack our fully assembled furniture.
To prevent further damage in transit and ensure our product arrives in top condition we reduce the transit time and limit the number of hands our furniture passes through. This includes using large shipping containers that are sent directly from the factory in Indonesia to our warehouse in Melbourne, which takes about 3-4 weeks. On arrival the cartons of furniture are loaded into the warehouse, ready to be picked for delivery to customers across Australia.
Our Australian delivery team form a carefully selected network of dedicated furniture carriers. It’s taken several months to manufacture and transport our furniture items to Australia, so we take extra care to make sure the last leg of the journey to your home is safe as possible.